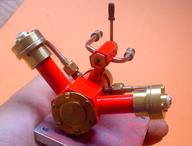
Comme je le disais, le moteur bi-cylindre dit de "Darnaud" m'a fait rêver. Voici l'occasion de le reproduire avec ... de la plomberie. On peut bien entendu utiliser un hexagonal mais l'usinage sera plus long et fera souffrir inutilement notre petit tour ...
La réalisation n'aura plus grand chose à voir avec le croquis ci-contre, mais le moteur lui ressemblera, aura la même distribution et ... fonctionnera !
Dans cet album,sont décrites les petites choses qui diffèrent avec les moteurs précédents sachant que le principe de construction est identique.
|
| |
|
 les moteurs dit de "Darnaud" | Ces moteurs étaient par la maison BABY-TRAIN, et ils ont fait rêver plus d'un modéliste ... dont moi qui ne pouvais pas m'en offrir un !
"J'ai bien connu ces moteurs qui étaient commercialisés par le magasin "la source des inventions", boulevard de Strasbourg à Paris dans les années 1965 environ pendant de nombreuses années . Ils etaient fabriqués en Savoie par une toute petite entreprise de décolletage . J'avais acheté en 1966 le mono cylindre et, monté dans l'Abeille 24, il marchait bien . Je dirai qu'il sont souples avec un bon ralenti ; par contre la consommation de vapeur avec le carter est importante."(Michel OLIVE) |
|
 | le monocylindre |
| 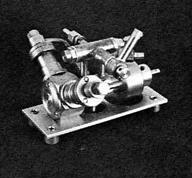 | le bi-cylindre |
| 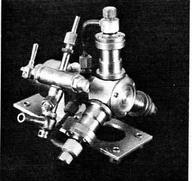 | en étoile |
| 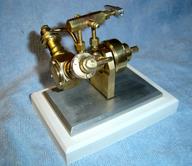 | le moteur construit par Max Rousseau |
|
|
quelques études de Patrick pour mieux comprendre le bi-cylindre |
|
|
|
 moteur "plombé" 3 | Cette fois, il s'agit d'un moteur avec deux cylindres calés à 120°.
|
|
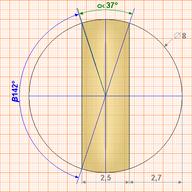 le bi-cylindre avec cylindres calés à 120° : un moteur qui pose problème
de part sa distribution car si on reprend les cotes du distributeur (rond de diamètre 8, plats de 2.7 de profondeur et trou d'alimentation de 2.5), en faisant les calculs comme dans la page des généralités, on obtient un angle d'admission de 179° identique à celui de l'échappement, soit 179° également.
Il n'y a donc pratiquement pas de fermeture et on passe presque directement de l'admission à l'échappement ...
Mais aussi par sa conception avec, au-dessous, un canal menant au carter et en contact alternativement avec l'admission et l'échappement ... Bien des suppositions sur la présence de cette ouverture !
|
|
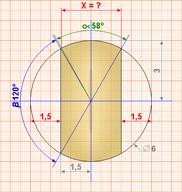 premières recherches
Elles visent à adapter les cotes de ce moteur à celle d'un modèle facile à exécuter et avec des éléments de ... plomberie : . le distributeur aura un diamètre de 6 mais respectera la disposition des plats et les encoches circulaires pour assurer le changement de rotation par inversion de l'admission et de l'échappement : hauteur des plats = 1.5 . perçage du trou d'admission ou d'échappement sur le corps à 2.9 . même conception que pour les "plombés 1 et 2 ", cependant la cylindrée sera ramenée à 1 cm3 et, pour l'obtenir avec deux cylindres, on utilisera du tube de 8 x 10 avec un piston de 8 tiré d'un rond de laiton . un inverseur sera ajouté si ... ça fonctionne ! Et, comme c'est tout bon, le plan de cet inverseur est ajouté en bas d'album.
Pour ces calculs, voir l'album sur les généralités : généralités |
|
On ne peut pas dire que ce soit un modèle de début car certaines cotes sont critiques, mais, les méthodes employées doivent permettre d'arriver à un bon résultat. |
|
|
| 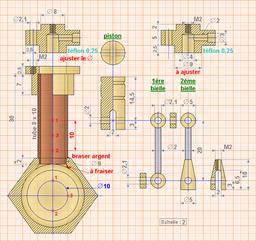 | Ces plans doivent être modulés en fonction des éléments de plomberie que l'on trouvera et que l'on utilisera ou non.
On peut aussi prévoir une cylindrée supérieure si on veut par exemple motorise une embarcation : 1.5 ou 2 cm3 en modifiant le diamètre du tube et par conséquent le piston ...
On peut finalement imaginer pas mal de modifications voire d'améliorations. |
|
|
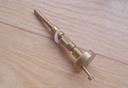
Il existe malheureusement une erreur sur ce plan et je ne m'en suis aperçu qu'en construisant le Plombé 4 : ici le maneton est calé à 180° et non à 90 comme c'est d'ailleurs expliqué par l'image lors de la construction. Une petite photo pour montrer où se situe le niveau de l'erreur : le maneton est dans le même plan que les plats. |
|
|
le corps
même méthode, mêmes dimensions que le "plombé 1". On pourrait cependant accroître la portée de l'axe distributeur en allongeant le rond qui vient s'insérer dans le mamelon et qui peut en dépasser par l'arrère, mais il faudra alors décaler les lumières.
Une différence : le carter sera bouché or la face présentée par le manchon n'est pas suffisante pour placer des vis . On va donc ajouter une collerette qui permettra le vissage d'un couvercle étanche. |
|
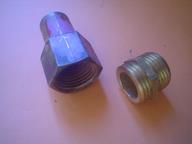 | le corps terminé par son manchon et un bout de mamelon |
| 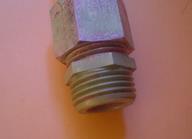 | brasage du mamelon sur 2 filets environ Pour être plus précis et pour n'avoir pas à reprendre les plans ensuite, mesurer une cote de 16 mm intérieur. |
| 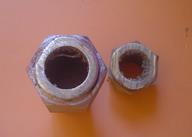 | sciage de l'excédent |
| 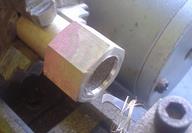 | dressage et alésage à diamètre 17 |
|
|
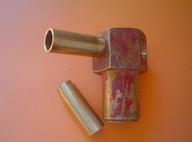 Une idée pour assurer le positionnement vertical du cylindre de diamètre extérieur 10 sur le manchon : . percer le manchon à 9 . au tour, reprendre la base du cylindre sur 2.5 mm au diamètre 9 > si on opère un assemblage bien juste, le cylindre tiendra seul lors de l'opération de brasage et sera bien vertical en appui sur le manchon
Cependant, triste expérience, ce n'est pas suffisant : il faut procéder cylindre par cylindre en le bloquant comme pour le moteur précédent et là ... ça coule tout seul (la brasure !). |
| |
|
Avant d'aller plus loin, il faut penser à la fermeture du carter qui devra être, cette fois, étanche. |
|
Rondelle de laiton de 2 mm d'épaisseur grossièrement découpée au diamètre 26 ; soudure à l'étain sur un tube de cuivre dont la face à souder a été reprise au tour ; mise au diamètre 24 et petit plat pour faire joli en ramenant à 1 d'épaisseur. |
|
Repérage des 6 trous de fixation avec le diviseur (on pourrait n'en mettre que 3) : pointage puis perçage à 1.2 à 1.5 mm du bord. |
|
Opération habituelle : repérage d'un trou, perçage, taraudage à M1.6, perçage du trou du couvercle à 1.8 puis serrage avant de repérer les autres trous sur le carter.
Attention, on va tomber dans la brasure et le foret de 1.2 ne va pas aimer. Pour le repérage, on peut se servir du foret mais, avant de percer pour le filetage, il faudra préparer le perçage en allant le plus loin possible avec le foret à centrer de diamètre 1 et en veillant à ce qu'il ne dévie pas ; et seulement ensuite, percer à 1.2. |
|
Et, ce qui devait arriver arrivât : une vis que j'ai voulu serrer lors d'un essai s'est cassée ... Comment faire ?
|
|
La solution d'urgence : serrage le mieux possible dans le gros étau de la grosse perceuse (en enlevant le volant) , pointage, perçage à 1.6 puis taraudage à M2. |
|
Pose d'un goujon M2 et nouvel essai. Mais ... ça fuit encore ! En fait, c'est tout bête : les taraudages débouchent dans le carter et la vapeur s'infiltre par le pas du filetage. Il faut donc trouver une autre solution ...
|
|
Solution que voici : remplacer les vis par des goujons de 1.6 mais, avant de les visser, les enduire de joint bleu ou, si vous n'en avez pas, comme moi, de frein filet. Il faut aussi dire que les goujons admettent un serrage plus important que les vis, surtout les toutes petites. De puis, étanchéité parfaite. La pose d'un premier goujon de 2 permet s'envisager le taraudage de tous les trous à M2; et ce sera mieux. |
|
Ou alors, cette autre solution à la quelle j'avais déjà pensé ...
|
|
A l'usage, il apparaît que le montage précédent est un peu fragile : on hésite toujours à serrer fortement des vis M1.6, or l'étanchéité du carter est primordiale ! Alors, une idée pour faciliter cette partie de la réalisation.
On ne touchera pas à l'alésage du mamelon qui fait environ 14.5 mm de diamètre mais on modifiera le disque de vilebrequin en amenant son diamètre à 14 mm de diamètre. Il faudra aussi modifier la vis de positionnement des têtes de bielles : on ne peut pas garder l'hexagonal que l'on ne pourra pas serrer, et il faut usiner la tête de cette vis avec une fente pour un serrage au tournevis ... |
|
|
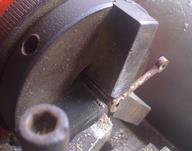 | reprise au tour d'une des biellettes : cette fois du rond de 2 fileté en bout et brasure ; on ramène l'épaisseur des ronds à 2 mm |
| 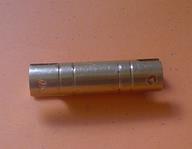 | Il est plus facile de les réaliser ensemble : une fois terminés, on les sépare et on les mettra à longueur lors du réglage |
| 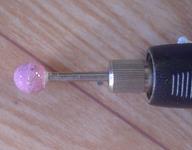 | Une fraise en forme de boule montée sur la perceuse est bien pratique pour obtenir l'évasement du manchon et du bas des cylindres. |
| 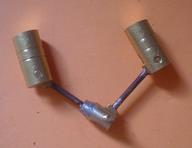 | Un premier essai m'a amené à meuler la chape double et lui donner une forme conique pour que rien ne frotte. Petit usinage à suivre ci-dessous : |
|
|
Rond de 6 de diamètre : percer à 1.6 dur 10 mm ; usiner à 30° ; et tarauder à M2 (taraud d'ébauche, on terminera ensuite). |
| Perçage de 2 tous de 2 mm de diamètre, bien dans l'axe. |
|
|
Fraiser. |
| Pas de déplacement latéral : desserrer l'étau, caler la pièce, serrer et percer à 2.1 mm. |
|
|
Il n'y a plus qu'à scier après avoir terminé le taraudage M2. |
| Cette pièce est fragile, elle ne sera pas brasée à l'argent mais soudée à l'étain (solidité garantie par le filetage), la partie supérieure étant traitée comme la première bielle. |
|
|
disque de vilebrequin
Cette fois, il sera vissé en bout du distributeur ... des idées de réglages à tester ! Cependant, comme il risque de se dévisser lors d'un changement de rotation, une vis de blocage M3 est ajoutée sur le disque : c'est pourquoi il est épais de 4 au lieu de 3 pour les autres moteurs. Mais ce n'est pas la solution idéale et il vaut mieux souder axe et disque de vilebrequin avant l'usinage. Je viens d'avoir un déréglage : vis mal bloquée sur le filetage ?
L'axe ou distributeur faisant 6 mm de diamètre, le disque est fileté à M5, pas normal afin d'accepter une vis standard qui va permettre de le maintenir. |
|
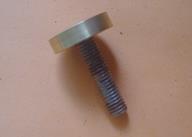 | le disque et sa vis ... |
| 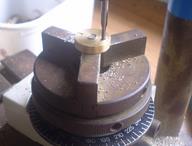 | ... on n'a aucun souci pour le taraudage perpendiculaire |
| 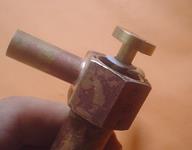 | préparer une rondelle de téflon de 0.5 |
| 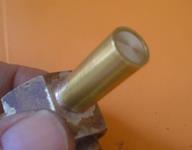 | et on peut procéder au réglage de la hauteur des pistons à 2/10ème du bord du cylindre |
|
|
distributeur
qui est réalisé dans un rond de laiton de 6 (de l'inox serait beaucoup mieux). |
|
réalisation des gorges de 2 de large et de 1.5 de profondeur : pour éviter toute vibration, réaliser la première gorge le rond de laiton le plus près possible du mandrin (si possible un porte-pince de 6), puis sortir la pièce pour la réalisation de la seconde gorge on peut en profiter pour abatte légèrement à la lime les bords avant de sortir la pièce |
|
réalisation des plats avec le calage précédemment utilisé Certes on pourrait utiliser le montage vertical du plateau diviseur et le porte-pince mais ...le mien vibre dans cette position et je n'ai pas eu le courage de fabriquer un support ! |
|
malgré le caractère artisanal de ce montage les résultats obtenus avec la descente fine sont bons sauf ... si on se trompe ! J'ai été amené à reprendre deux fois une rainure et le calage a toujours été respecté avec une petite astuce supplémentaire : avant le démontage, ne jamais bouger la fraise dans sa dernière position de travail : elle servira au calage de la pièce lors du remontage. |
|
perçage du corps
Une petite opération délicate sauf si on peut caler le corps afin que les perçages de fassent bien perpendiculairement et à 120° pour ceux d'alimentation à 2.9. Comme pour les moteurs précédents, le traçage a été effectué longitudinalement avec l'outil à centrer, et, en partant cette fois de l'extrémité du corps, on termine ce traçage sur le marbre (cotes sur le croquis) |
|
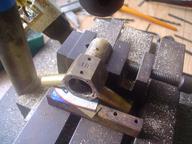 | position à plat |
| 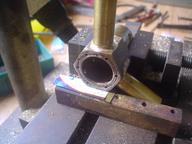 | position à 120° |
| Si le traçage longitudinal est correct, on n'aura aucun problème pour ces perçages à 60 ou 120° en prenant pour référence un des plats de l'hexagonal.
Sur les photos, on voit le calage : plat dans l'étau pour le rond et calage supplémentaire en bout et bien plat pour l'hexago.
Sur la première photo, outre les trous de fixation déjà percés sur le manchon, perçage du trou qui mènera au canal inférieur que l'on percera de l'intérieur : pas facile, il faut se servir du trou central pour glisser le foret dans le mandrin ... Ce trou percé à 2.5 sera taraudé à M3 pour être bouché partiellement par une vis. On pourrait aussi ne pas fileter et souder un bout de rond à l'étain. Mais je voulais voir si le moteur tournait sans ce canal inférieur et le filetage servait à le boucher entièrement. |
|
|
les premiers essais
Ils ont eu lieu au compresseur. Le moteur abondamment garni d'huile dans les cylindres et le corps via les ouvertures menant aux cylindres n'a pas tardé à tourner mais dans un sens seulement faute d'inverseur. Petit essai en collant la pipe d'alimentation du compresseur au trou d'échappement et ça tourne dans l'autre sens à une pression vraiment minime.
Observations : . le carter doit être parfaitement étanche, sinon le moteur tourne au ralenti . il faut boucher avec le doigt les trous de fixation sinon idem . en bouchant complètement le canal inférieur, idem
Et ... au premier essai ce moteur ne démarre pas seul, il faut donner une très légère impulsion au volant. Par contre, en décalant un peu la position de ce volant, on obtient un démarrage franc et sans aide extérieure !
Alors, démontage, essais de calages du maneton par rapports aux plats ... Rien, si ce n'est que le moteur démarre si on l'aide mais tourne moins vite.
Alors, re-démontage et vérifications : en mesurant la distance entre les lèvres du distributeur, on constate que d'un côté la cote de 3 mm est bien respectée mais que sur l'autre on trouve 3.15 ! - en fait je m'en étais aperçu mais comptait sur la chance du débutant pressé - Petit passage à la fraiseuse pour reprendre cette lèvre, recalage du maneton bien dans l'axe, branchement et ...la suite en vidéo.
|
| |
|
 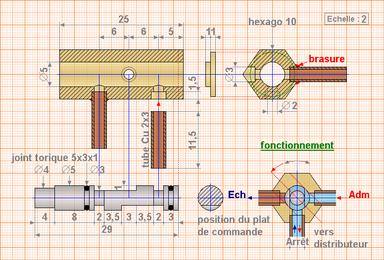 l'inverseur
Le principe est le même que celui du moteur dit de "Darnaud", mais toujours simplifié.
Le corps est un hexagonal de 10 que l'on percera à 4.8 avant de passer après les perçages latéraux l'alésoir de 5, le boisseau est un rond de 5 dont l'étanchéité sera obtenue par 2 joints toriques de 5 x 3 x1 . L'inversion d'admission de la vapeur et de l'échappement est assurée par 2 plats et 2 rainures circulaires.
Toutes les tubulures en cuivre de 2 x 3 sont brasées à l'argent sinon on aura des problèmes lors de la soudure à l'étain du bouchon et sur le corps du moteur.
Rodage à l'huile. |
|
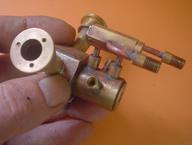 | position du distributeur sur le corps du moteur |
| 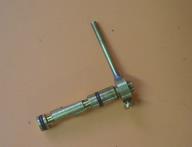 | le boisseau et sa tige de commande |
| 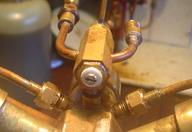 | on peut éviter le déplacement latéral en plaçant une vis en bout |
|
|
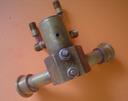 Et, avant de procéder aux essais, ne pas oublier de boucher les trous du carter : goujon M3 avec rondelle de téflon. A refaire, je souderai ces goujons à l'étain...
Et ne pas oublier de boucher le trou du corps avec une vis et une rondelle de téflon, mais sans boucher le canal inférieur ! |
|
 les essais à la vapeur | Ils ont déjà eu lieu, mais sans l'inverseur.
On remplit le graisseur de la chaudière d'essai, à 1 bar, on ouvre la vanne de la chaudière, on actionne l'inverseur et on tourne le volant à la main pour "chauffer la bête". On monte la pression à 1.5 bar et ... c'est parti ! Ce ne sera pas probant au début et il faudra actionner l'inverseur d'un côté et de l'autre mais, le graissage faisant, le moteur va démarrer seul et dans un sens et dans l'autre.
Une bonne surprise: Ce moteur tourne facilement et vite à 1 bar, l'inversion se fait facilement. A la fin de l'essai, j'ai arrêté la chaudière et il a gentiment tourné jusqu'à ... plus de vapeur !
Petites remarques : . à chaque démontage, nettoyer soigneusement les cylindres, les alésages du corps du moteur et de l'inverseur, essuyer et huiler avant remontage le distributeur et le boisseau : la moindre limaille va détériorer rapidement le moteur et le fonctionnement en pâtira . vérifier l'étanchéité du carter, celle des trous de fixation et de l'évent inférieur . compléter le niveau d'huile dans le graisseur : à ce propos, lors de la construction d'un graisseur spécifique pour ce moteur, le trou d'admission de la vapeur aura 0.8 mm de diamètre pour assurer le graissage maximum
|
| |
|
améliorations possibles
Mes moteurs sont souvent l'aboutissement d'une recherche, pour voir si la théorie s'accorde avec les plans qui en sont issus. Bien que certains tournent souvent sans présenter de réelles traces d'usure, on peut préparer une longévité accrue en : . réalisant le distributeur et le boisseau en inox . en ajoutant des segments de téflon aux pistons
prochaine étape
. le passer au banc d'essai et voir à combien il tourne et quelle est sa puissance . construire un réducteur qui lui sera accouplé pour voir s'il est capable d'entraîner un véhicule ... Et c'est fait ! |
|
Et l'aventure se termine : |
|
Voici la mouture finale avec l'ajout d'u réducteur.
Moyenne des puissances obtenues avec, il faut le rappeler un bi-cylindre d'1 cm3 seulement : . à 1.2 bar : 1.85 watts pour 320 tours/minute . à 1 bar : 1.37 watts pour 280 tours/minute . à 0.8 bar, 0.62 watts pour 200 tours/minute . à 0.5 bar, 0.43 watts pour 160 tours minute
Les essais ne vont jamais jusqu'à l'arrêt complet du moteur ... et, à titre de comparaison, pour mon oscillant de 3.6 cm3, j'obtenais à 0.5 bar une puissance de 0.80 watts à 600 tours/minute !
Pour la construction du réducteur, voir ce nouvel album :
Comment "muscler" un moteur ? |
|
des petits "trucs" réalisés depuis : |
|
. les goujons M1.6 ont été remplacés par des goujons M2 . les premiers filets de ces goujons ont été enduits de joint silicone résistant aux hautes températures
. les vis de fixation ont été soudées à l'étain
> plus aucune fuite, donc un rendement meilleur |
|
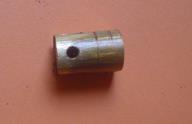 Ce petit moteur tourne très vite et l'usure des pistons me semble trop importante. Si on observe attentivement la photo, on voit que certaines rainures sont en train de disparaître ...
Et, comme je n'ai pas envie d'en usiner de nouveaux, voilà la solution adoptée : . coupelle de téflon en partie supérieure : réduction de la hauteur du piston de 2 mm pour placer une rondelle et la coupelle qui sera vissée en bout. Pas de problème pour la coupelle puisqu'elle se trouve dans le bon sens pour la mise en place. . diminution du diamètre du piston sur 2 de largeur et 1.2 de profondeur pour un enroulage de téflon qui sera bloqué en partie supérieure par la coupelle. |
|
Un premier essai avec une seule coupelle par piston : problème, il est difficile de placer la seconde nécessaire quand on se trouve avec un double-effet ...
Lors du remontage, je n'ai pas placé immédiatement les culasses et ai envoyé de l'air : les pistons remontent bien sous l'action de la pression qui arrive par le canal inférieur ! |
| En haut un piston totalement modifié, en bas le second en préparation.
Cette fois plus aucun problème. Certes, une nouvelle fois ce n'est pas très orthodoxe, mais certains utilisent le ruban de téflon pour garnir une ou deux rainures ! |
|
|
  album terminéDes erreurs ? Des commentaires ? Des questions ? ... écrivez-moi |
| | | | |
|