Et voici le suivant 20 années plus tard. Probablement mieux conçu ...
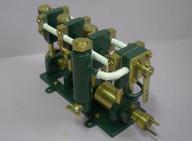
Après la remise en état du mon premier moteur de ce type, une envie de le reconstruire en essayant de l'améliorer.
Le résultat, pour l'instant, semble plus que correct et cette fois il ne faudra pas attendre une vingtaine d'années pour le voir fonctionner à la vapeur ...
A peine essayé à l'air comprimé qu'on passe à la vapeur : pas encore d'inverseur, essai fait sans rodage ni graisseur ! |
| |
|
 plan d'un des moteurs et distribution | Comme d'habitude, ce plan peut être modifié, il ne s'agit que d'une méthode ...
Ainsi, avec des cylindres de diamètre 8, on obtient une cylindrée de 2.1 cm3 (2), mais si on les remplace par des cylindres de diamètre intérieur 10, on obtiendra une cylindrée de 3.3 cm3 avec la même distribution et la course de 1.4 cm. |
|
| 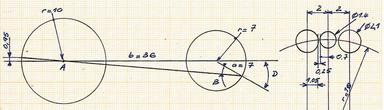 | Ainsi conçu, ce moteur devrait démarrer très facilement : l'angle D ne fait que 35° et la fermeture totale est de 70°.
Il ne présente pas vraiment de difficultés à construire sinon que cela revient à construire trois moteurs au lieu d'un. Il faudra seulement veiller lors des usinages à bien caler les pièces pour obtenir au final une bonne verticalité des supports. |
|
|
 l'embiellage | le vilebrequin
Il va falloir caler les manetons à 120° . |
|
| 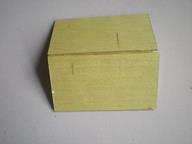 A gauche, un croquis pour le repérage des joues du vilebrequin. On y trouve également les données pour l'usinage de la platine du moteur.
La forme pour le calage est en contreplaqué : faces à 120°. Sur le dessus on aperçoit les repères effectués en partant du croquis. |
|
|
Le volant de diamètre 20 percé à 3 avec le filetage M2 devant recevoir le maneton qui n'est pas encore coupé à dimension et qui doit mesurer environ 5 cm. A côté l'axe du vilebrequin dont on a préparé le plat devant recevoir la vis de blocage : le plat ne va pas jusqu'à l'extrémité , on laisse 1/2 mm de rond qui empêchera le volant de sortir. |
| Perçage en série de la barre de laiton de 15 x 4 : trous de diamètre 3 distants de 7 mm. Sur le sommet, perçage à 1.6 et taraudage à M2 pour le futur blocage. |
|
|
Là, c'est brut de sciage mais, les trous ayant été percés en déplaçant le chariot de la perceuse, aucun problème d'entre axe. Pour les perçages, vérifier au préalable que le porte mandrin de la perceuse est bien perpendiculaire ... |
| Mise à épaisseur des joues : 6 mm. Il est vrai qu'on n'obtiendra pas avec ce montage des faces totalement parallèles. Il faut serrer l'étau et donner un coup de marteau avant l'usinage. |
|
|
Premier montage : le maneton est vissé à l'envers sur le volant mis en position. On enfile les ronds de 3 qui seront les futurs manetons et, une fois le serrage effectué, cela devrait se maintenir en place. |
| Positionnement sur le gabarit à 120° après un ponçage sérieux des axes et des joues.
Mise en place des joues distantes de 6 mm selon les repères. La tige du maneton doit se trouver à l'aplomb de l'arête du gabarit. Bloquer quand tout est en place. |
|
|
Et on obtient un ensemble rigide ...
Pas de papier alu sur le support qui risquerait de na plus être réutilisable comme lors de la première réalisation ! |
| ... qu'il reste à souder à l'étain.
Présenter le fil d'étain à l'extérieur des joues pour ne pas empâter l'intérieur.
On pourrait aussi braser à l'argent ... |
|
|
Après sciage, le vilebrequin est prêt à servir. |
|
les chapes
tirées de la même barre. |
|
Toujours le même traçage puis le perçage en série : . trous de diamètre 3 au centre pour recevoir le maneton . et trous latéraux de 3 également pour faciliter l'usinage des arrondis. |
| Opération de sciage. La patte supérieure sera réduite ensuite. |
|
|
L'arrondi de 3 est réalisé avec une fraise hémisphérique de diamètre 6 normalement réservée au bois ... |
| Reprendre la base pour obtenir une cote de 3 à partir du centre de l'axe.
Puis perçage à 1.6 sur toute l'épaisseur avant de terminer par une reprise à diamètre 2 sur 3 de profondeur |
|
|
Taraudage à M2. |
| Opération de repérage avec une petite fraise ... de dentiste. |
|
|
Et, pour presque terminer, sciage.
Cette fois, pas de scie fine toujours approximative mais utilisation d'une fraise-scie pour laquelle un porte-scie a été fabriqué. Petit outillage facile à réaliser qu'on trouvera en allant sur ce lien : petit outillage - 17 |
| Il ne restera plus qu'à percer puis tarauder pour la tige du piston. Petit repérage à la lime de la position de l'axe. |
|
|
 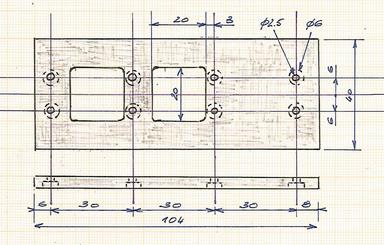 socle, supportsLe socle de 104 x 40 est en alu de 3 d'épaisseur. Les perçages qui vont recevoir les vis M2 de longueur sont de 2.5. Les supports, ou tout au moins leur base sont en alu de 6 (pour le dessin, voir le premier croquis). Là aussi il faudra les repérer par pointage.
|
|
Tous les supports sont percés au départ à diamètre 3 ce qui va faciliter les usinages.
Le 1 et le 3 seront repris à diamètre 6 sur une profondeur de 2.5 ( roulement de 30.60.25); le trou de 3 sera ensuite repris à 3.2. Le 2 sera repercé à diamètre 5 et la partie supérieure sera découpée pour permettre le passage de l'arbre du vilebrequin au montage. Le 4 sera repercé à 3.2. Pas de roulement pour lui car l'alignement de 3 roulements n'est pas facile. Par contre, au montage final, on ajoutera un roulement dans une cage réglable en position qui permettra un fonctionnement parfait (il faut toujours espérer !). . |
| Premier essai : le vilebrequin doit tourner très librement en donnant une impulsion. |
|
|
Une idée pour la fixation future du moteur sur un plateau de véhicule ou dans le fond d'une coque : l'ajout de pattes de fixation.
Pour cela on prépare leur emplacement à la fraise : 8 de large sur 1.5 de profondeur. La socle est à nouveau fixé sur son carré pour la mise en place dans l'étau : 3 vis de blocage cette fois car les efforts transversaux sont importants.
|
|
Vue de dessous : utilisation de vis à tête fraisée M2 de longueur 6 qui ne dépasseront pas au-dessous. Les pattes sont tirées d'alu de 1.5 d'épaisseur. L'arrondi est obtenu à la meule puis à la lime. Perçage de trous de diamètre 3. |
| Vue de dessus : la vis M2 dépasse suffisamment pour placer l'écrou.
On peut procéder autrement pour obtenir un aspect fonderie : même montage mais taraudage dans le socle et vis de longueur 4 que l'on raccourcira à 3. Une fois les vis en place, on bouche les trous avec de l'araldite. Inconvénient cependant pour le démontage si on doit modifier la longueur des pattes ... |
|
|
 |
cylindre
Aucune difficulté sinon, l'ajout d'une bague au bas du tube pour faire joli ! |
| Ces bagues font environ 1 mm d'épaisseur et impossible (pour moi) de les tronçonner dans un tube de 10 x 12 ... Alors, un coup d'outil à tronçonner pour amorcer une rainure et ensuite sciage à la scie fine. |
|
|
Enfiler la bague obtenue sur un rond de 10. Cela ne va pas tenir au tournage et il faut donner un léger coup de soudure à l'étain. |
| Il ne reste plus qu'à reprendre au tour pour arriver à la bonne épaisseur, puis chauffer et enlever la bague terminée. |
|
|
| Par contre le maintien de la pièce est plus facilement obtenu avec cette pince qu'avec du fil de fer. |
|
|
Reprise des côtés : le sabot fait 15 de largeur, on a donc de la marge. Si le cylindre a bien été disposé dans la rainure du sabot, l'écart est de l'ordre du dizième. |
| Traçage puis perçage des trous de 1.4 et 2.5 (pour taraudage à M3). Ensuite, passage de l'alésoir. |
|
|
Finition : soudure à l'étain du bouchon supérieur et de la bague pour faire joli.
|
| Une idée pour dissimuler un peu la vis de blocage (M1.6) du guide de la tige de piston. Pas facile à mettre en place cette vis sauf avec la v"visseuse" maison !. Un coup de lime pour supprimer toute bavure nuisible aux coupelles de téflon. |
|
|
glace
Elles sont tirées de plat de laiton de 6 d'épaisseur.
|
| Il faut surtout se montrer attentif lors des perçages. Là aussi bien effectuer les montages dans l'étau et, indispensable le pinceau qu'on passe après chaque opération : la moindre limaille risquant de décaler notre pièce. |
|
|
Les trois glaces obtenues avec les perçages des différentes faces. |
| Un premier montage pour se faire plaisir. |
|
|
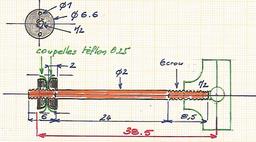 piston
Il est à coupelles de téflon. Certes, une seule coupelle suffirait mais la seconde participe au guidage ...
|
|
Le voici monté avec ses coupelles, la bague de guidage qui sera bloquée par la vis en bas de cylindre, sa chape et l'écrou de blocage. |
| Petite opération de réglage en situation : . le piston vient buter sur la tige d'épingle, on règle l'axe de la chape à 38.5 mm et on bloque l'écrou. |
|
|
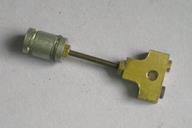
On peut aussi envisager la solution d'un piston comme celui-ci : rond d'alu (du laiton serait mieux)coulissant parfaitement dans le cylindre avec deux gorges et enroulements de téflon en ruban. Je n'ai pas poursuivi l'expérience car mon piston était trop court : il lui faudrait au moins une longueur de 15 pour qu'il soit correctement guidé. C'est envisageable, même si il sort du cylindre en position de PMB. |
|
 |
Pour obtenir nos trois moteurs, il ne reste plus qu'à, dans du rond de laiton de 5, usiner les 6 jambettes.
Le montage se fait à l'aide de vis qui traversent les supports. A chaque serrage il faut vérifier que le vilebrequin tourne librement.
Fonctionnement plutôt sympathique ... Il ne reste plus qu'à monter le reste. |
| |
|
 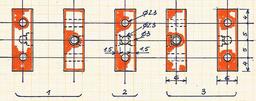 les tubuluresOn utilisera du carré de laiton de 6 x 6 et du tube de cuivre de 2 x 3. La seule difficulté étant le repérage car les raccords des extrémités sont percés différemment. Deux forets à utiliser : 2.3 et 3.
Pour chaque raccord, percer à 3 sur une profondeur de 1.5 afin de bloquer le tube de cuivre lors de l'emboîtement. |
|
Contrôle de l'alignement avec un réglet. Logiquement en ayant percé à 2.3 on n'a aucun problème. |
| Un petit truc : lors du montage des trois premières glaces, il faudra veiller à ce que le raccord soit légèrement en retrait sinon s'il n'est pas parfaitement aligné avec la glace ou déborde vers l'avant, le sabot va venir buter et s'écartera de la glace.
Lors du perçage des trous de fixation on peut après réglage décaler d'un ou deux dizièmes le centrage mais le perçage à 2.3 est normalement suffisant. |
|
|
Mise à longueur des tubes de cuivre. |
| Il est loin le temps où on trouvait des tubes faisant vraiment 3 de diamètre !
Faute de tube en laiton parfaitement calibré, il a fallu reprendre toutes les extrémités des tubes à l'aide d'un lime : reprise sur 2 mm environ avec essais pour que ça entre en forçant un peu. |
|
|
Un petit truc pour ne pas se tromper dans les perçages : repérer les raccords avec une flèche et marquer ceux des extrémités à l'intérieur d'un cercle.
|
| 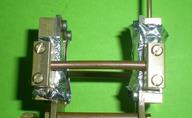 Et puis, il n'y a plus qu'à souder ... à l'étain. Effectuer le montage en plaçant entre les glaces et les raccords du papier alu, vérifier qu'aucun tube ne bouge et souder légèrement.
Méthode déjà utilisée pour cet autre moteur. |
|
|
les joints
On peut les fabriquer en série. |
|
Découper dans du téflon de 0.25 une bande de 6 mm de large, la présenter sur les trous de la glace et pointer fortement pour pénétrer dan les trous. |
| Se servir de l'empreinte pour donner un coup d'emporte-pièces de 2. |
|
|
Lors du montage final, il est possible que les joints se placent un peu de travers et débordent de la glace. Un coup de cutter pour les ramener à ras du raccord empêchera tout problème de cohabitation avec le sabot..
|
|
 montage | Les supports ne seront pas bloqués, à peine serrés. Ce n'est qu'une fois les tubulures en place et serrées que, si le vilebrequin tourne correctement on procédera à leur serrage définitif. |
| Commencer par le 4 qui va recevoir -plus tard- l'inverseur. |
|
|
On fait suivre de 3 ... |
| ... suivi des derniers. |
|
|
Au premier essai, l'un des écrous s'est dévissé ! Petite solution rapidement mise en place : percer un écrou de 3 pour y placer une vis M1.6 ... |
| Une fois le bon plaquage obtenu, il suffit de bloquer la vis. |
|
|
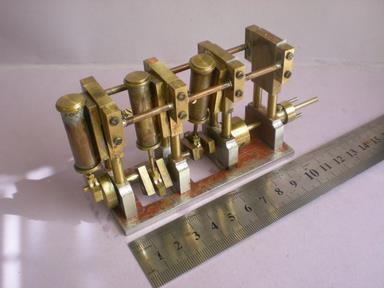 | Pour ce montage, utilisation de ressorts pour le plaquage du sabot. |
| 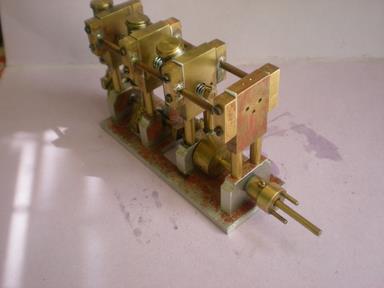 | A l'avant viendra se placer l'inverseur |
|
|
 |
|
 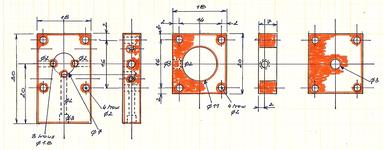 l'inverseur de ce tri-cylindreIl est d'un type déjà construit pour le tri-cylindre précédent ou encore le moteur du Gulnare.
Le corps est tiré d'un carré de 20 x 20. La méthode d'usinage décrite permet d'être certain que les trous du bâti et de l'inverseur vont se trouver exactement les uns en face des autres et d'obtenir une vitesse égale dans les deux sens.
|
|
Perçages du bâti . |
| La réalisation du corps se fait par perçage à diamètre 11 ce qui n'est pas évident si la pièce n'est pas bridée. Aussi, sans bridage, par perçages successifs je suis arrivé à 11 mais le décalage constaté a été rattrapé lors de l'ajustement à la cote 18 en largeur.
Les trous de fixation sont obtenus par superposition du bâti : ainsi on pourra utiliser de vis M2 sans avoir à agrandir les trous.
|
|
|
Les observateurs verront que mon corps fait 18 x 18. Les plans ont été modifiés en 18 x 20 pour faciliter le perçage des trous qui ne doivent pas déboucher dans ceux servant à la fixation de la tubulure sur les côtés du bâti.
Ici avec ce carré de 18 x 18, petit problème pour une vis du bas : la vis latérale si elle est placée avant la bloque !
|
| Solution : cette vis est légèrement modifiée à la lime dégageant ainsi le passage ... |
|
|
L'inverseur : prendre un rond de 12 de 6 ou 7 de longueur, le percer à 3 et y souder à l'étain un rond de 3 après perçage. |
| Reprendre le rond de 12 et l'amener au diamètre 11 pour qu'il vienne glisser dans le corps. |
|
|
Le futur inverseur est en place dans le corps; sur le côté le couvercle en tôle de laiton de 2 découpé pour déborder de 1 ou 2 mm sur les bords du corps après perçage à diamètre 3. |
| Montage obtenu : il n'y a aucun jeu et l'inverseur est parfaitement centré. Il restera en place pendant tous les perçages.
Le perçage se fera par superposition : percer un trou en s'aidant du corps, placer une vis et son écrou, percer les autres tous ...
|
|
|
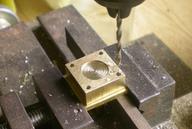 premier trou |
| 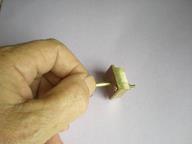 | blocage |
| 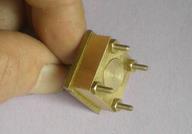 | montage |
| 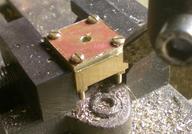 | finition |
|
|
Amener l'inverseur à ses cotes : diamètre 10.6 et épaisseur 3. On termine par le chanfrein. |
| Perçages à travers l'inverseur de 1.8 et saignée profonde de 1.5 : le sourire de l'inverseur ! |
|
|
Les deux joints : celui du bâti et celui du couvercle. Il faudra glisser l'inverseur à travers le second pour le montage. Sans oublier de glisser sur le rond de 3 un bout de silicone plus long d'1 mm que la hauteur du corps. Ce bout de silicone va s'écraser et faire étanchéité. Cependant, il faut le couper bien d'équerre ! |
| Perçage du corps pour l'arrivée de vapeur. Le tube de 2 x 3 est brasé à l'argent sur le corps et on utilise de l'étain pour la fixation du graisseur. Calculer la longueur du tube de raccordement pour que le graisseur arrive entre les bâtis 3 et 4 sinon impossible de visser les tubulures. |
|
|
Sortie vapeur avec un tube de 2 x 3 qui "s'enroule" autour du montant.
Soudure argent car il va falloir souder ensuite un raccord à l'étain. |
| Le bâti 4 est prêt pour le montage. |
|
|
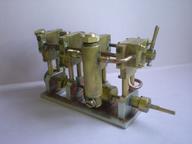
Montage complet avant les essais de l'inverseur ... |
|
 |
|
 |
Une bague de 8 de diamètre et percée à 3 : épaisseur de 5 pour venir retenir le roulement du bâti 1. On ajoutera une rondelle de téflon entre les deux. Un volant de 20 de diamètre et de 22 de long qui est inutile mais qui comble un vide et sert à retenir le roulement du bâti 3. Là aussi rondelle de téflon entre les deux.
|
|
levier d'inverseur percé de trous de diamètre 1.5 pour une éventuelle radio commande. |
| On obtiendra un alignement correct en procédant ainsi : . traverser le rond percé à 3 avec un foret de 1.6 . faire une encoche de 1.5 de large puis sorti de l'étau . tarauder du côté opposé de l'encoche à M2 . braser le plat de 1.5.
|
|
|
porte roulement pour le bâti 4 : pour l'instant ce bâti a été percé à 3.2 et le vilebrequin repose sur les roulements des bâtis 1 et 3 ce qui assure une rotation parfaite. Mais, lorsque le moteur sera relié à un autre arbre, le roulement du bâti 3 va terriblement souffrir ... Il faut donc ajouter un autre roulement dont la position sera réglable et qu'on pourra donc aligner au mieux avec les deux autres. |
|
Usinage d'un rond d'alu de diamètre 20 que l'on perce à 3.5 et qu'on reprend au diamètre du roulement en tenant compte de son épaisseur (ici diamètre 7 sur une profondeur de 2.2 pour un roulement épais de 2.
|
| Usinage extérieur pour une épaisseur de 5. |
|
|
Perçages à 2.5 sur un axe que l'on a tracé à l'outil lors de la première opération. |
| Le bas du bâti 4 est taraudé à M2. Le trou du haut du porte roulement est repris en forme de lumière. Le déplacement du roulement pourra donc se faire latéralement et en hauteur. En fait il s'agit d'un réglage de l'ordre du 1/10 ème. |
|
|
Cachez donc ces ressorts que je ne saurais voir ! Tube de 7 x 8 soudé à l'étain sur un feuille de laiton de 0.5, reprise au tour, perçage, mise à longueur ... |
| Une autre idée pour la fixation des tubulures : des goujons qui vont faciliter le montage et maintenir les joints en bonne position. |
|
|
Petites baguettes de bois exotique pour les cylindres : collage à l'araldite pour métaux. Ponçage puis passage de l'ensemble au miror. Le bois supporte bien en se teintant un peu. |
| Montage d'un cylindre sur son bâti et ... on ne voit plus le ressort. |
|
|
 Montage final | Toutes les pièces ont été démontées, certaines ont été peintes, d'autres passées au miror Les cylindres sont habillés de bois. |
|
préparation des 4 bâtis
|
| 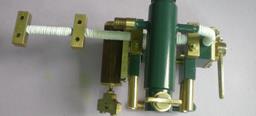 | montage de la tubulure de droite |
| 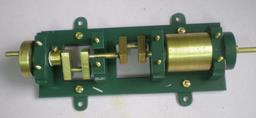 | montage du vilebrequin |
|
|
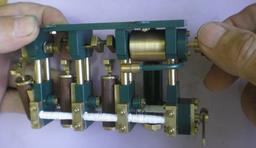 réglage de la rotation du vilebrequin
On retourne le moteur alors que les pistons sont débarrassés de la partie basse des chapes. Les tubulures sont serrées et normalement sont à la bonne place étant donné leur mode de soudure.
On commence par serrer par le dessous le bâti 4, puis le bâti 1. On tourne ... Puis on serre le bâti 3. On tourne ... Puis le porte roulement du bâti 4. On tourne ... Et enfin le bâti 2, et plus besoin de tourner.
En disant "on tourne", il s'agit de faire tourner librement et plusieurs fois par lancement . |
|
 |
|
|
 Un jour, je le testerai et les résultats étonneront quant à sa puissance mais pour cela il me manque une pile minuscule pour le compteur de vitesse qu'on ne trouve pas ici ... |
|
 |
 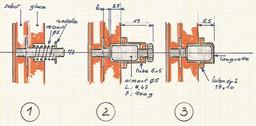 petite expérienceque celle du plaquage des sabots sur la glace avec des aimants.
En 1, le montage classique avec ressort.
En 2 , un montage déjà expérimenté avec vis d'acier de réglage d'entrefer.
En 3, une autre solution pour palier le manque de place pour utiliser la solution précédente. L'entrefer sera réglé grâce au perçage qui maintient l'aimant à quelques dizièmes de l'axe du sabot. |
|
Voici les trois modèles réalisés et testés. Comme dit, le premier prend trop de place et pourrait servir pour un autre oscillant solitaire, et on va voir comment réaliser et régler le dernier. |
|
En fait, en construisant le moteur, il était facile de prévoir l'emplacement d'un aimant de diamètre 5, de longueur 8.47 et de force 900 grammes. Le diamètre de l'aimant est le même que celui du ressort. Il faut cependant ajouter (en vert sur le plan d'ensemble) 2 trous M2 au dos de la glace. |
|
On devine l'aimant enfermé dans sa cage réalisée avec du tube laiton 5 x 6 où l'aimant coulisse. Cette cage est soudée à l'étain dans un plat de laiton de 2 d'épaisseur et de 10 de large percé à 6. Prévoir une petite languette pour empêcher l'aimant de sortir par l'arrière ... bien que, la force d'attraction ! |
| Le sciage d'un tube mince pose déjà problème (il faut le tourner sur lui-même plusieurs fois pour le présenter à la lame de scie) mais celui de la languette ne peut se faire que sur la longueur comme sur la photo. |
|
|
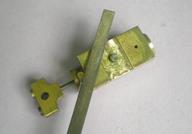 réglage de l'entrefer
Le pivot est un bout de vis en acier (pas d'inox) que l'on a scié pour arriver à la sortie du trou de 2 sur la glace. On présente l'aimant et on lime la tête de cette vis pour réserver entre la face de l'aimant bloqué dans le trou de 6 un espace de ... un ou deux dizièmes. Apprécier la fin du réglage en présentant le sabot sur la glace. Il faut que l'attirance soit maximum. |
|
|
|
Quel type choisir : ressort ou aimant ? Je crois que je vais rester dans le traditionnel avec le ressort car, en regardant de plus près la notice on s'aperçoit que ces aimants en néodyne ne gardent toutes leurs propriétés que si on ne dépasse pas les 80° ! Il en existe d'autres en ferrite acceptant 250° mais ils ne sont pas cylindriques. Dommage ! Or la température va être plus élevée que 80°... et combien de temps notre aimant va-t-il garder ses propriétés ? Par contre, les essais avec de l'huile ou encore de la graisse semblent ne rien altérer de leur qualité .
|
|
|
 mes amis construisent ... | ce moteur.
En voici un usiné par Phlippe TAQUET, moteur accompagné d'une chaudière de son cru : une "bouilloire" comme on l'appelle chez lui, au Canada ! |
| | |
|
 |
Franz
(Autriche) me fait parvenir un magnifique tutoriel pour la construction d'un moteur oscillant tri-cylindre
Certes ce n'est pas mon moteur mais il lui ressemble étrangement. Franz me fait l'amabilité de compliments :.
"Bonjour ami machine à vapeur, je suis très intéressé par les machines à vapeur ou chaudières à vapeur depuis longtemps. Ensuite, j'ai découvert votre page d'accueil et j'ai pris quelques conseils. Très belle et instructive page que vous avez. Maintenant, le désir de construire m'a attrapé et m'a fait utiliser la machine à vapeur 3 cylindres Oszilierende comme modèle. Merci pour tous les conseils. Sans cela, j'aurais dû tester beaucoup plus. Avec mes meilleures salutations d'Autriche."
|
|
|
|
  album terminéDes erreurs ? Des commentaires ? Des questions ? ... écrivez-moi |
| | | | |
|